The Task
As a result of numerous innovations in vehicle technology, electronic control units (ECUs) for the automotive industry are becoming increasingly complex and contain more and more software functionalities. Suppliers and OEMs need efficient methods for developing and testing these ECUs. One typical test step is component testing, in which an individual ECU is tested for functional correctness. These tests often take place on a hardware-in-the-loop (HIL) simulator or in a real vehicle and typically also include software integration testing of the ECU.
In contrast to unit tests, in which functions are tested individually, software integration testing focuses on the overall functionality of the control unit. The real ECU target hardware is not necessarily required when it comes to validating software integration. Using virtual electronic control units (V-ECUs), you can test the software functions conveniently on a PC or in the cloud on parallel computing nodes.
Motivation for SIL Tests and Challenges for Suppliers and OEMs
Why perform ECU integration testing in a SIL environment?
A software-in-the-loop (SIL) environment lets you test ECU software even before the corresponding ECU hardware is available. This allows you to frontload some essential test steps in the development process. SIL tests can also be a useful addition to established HIL test procedures later in the development process: As HIL systems are only available to a limited extent, SIL tests can help significantly increase test capacity.
A SIL environment can offer the following further benefits for integration testing:
- Tests can be carried out automatically and flexibly after each software change in order to obtain prompt and continuous quality statements about the software integration.
- Access to the SIL tests is possible at any time and from any location, as no special hardware is required to carry out the tests.
- Software developers can reproduce failed tests themselves at their own workplace. The debugging option further simplifies troubleshooting.
Which challenges do suppliers and OEMs have to meet?
When OEMs or suppliers want to introduce a SIL environment, they must first set up the test system in this environment. A key step in this process is the virtualization of the system under test (SUT), i.e., the creation of a virtual ECU (V-ECU) that contains large parts of the production software for the real ECU. Many components of existing HIL test systems can be reused for the SIL test systems, such as existing plant models or test tools. The same applies to existing tests.
As soon as the tests run in SIL, they can be automated and integrated into existing processes. Here, it is important that new software versions are transferred to the simulation system as automatically as possible and that the tests are then initiated.

The dSPACE Solution for SIL ECU Integration Testing
When it comes to software-in-the-loop (SIL) testing, dSPACE VEOS is the simulation platform that executes the virtual ECU (V-ECU) and models time-synchronously and simulates the communication between the simulation participants.
For plant and restbus simulations, VEOS can execute a wide variety of models, such as Simulink® models (SICs), dSPACE restbus models (BSCs), or Functional Mock-up Units (FMUs), and thus reuse the artifacts from the HIL tests.
All test tools that support the XIL API can also be easily reused. In this way, you can reuse all HIL tests, that relate purely to the software, in the SIL environment.
dSPACE Solution for V-ECUs
Your system under test is not yet available in virtual form for the SIL environment? Or you already have a virtual control unit that needs to be integrated into the SIL environment? Or perhaps you need support when it comes to accessing your V-ECU in the SIL environment? No matter what your current situation is:
Benefit from our comprehensive support for virtual control units.
These are just some of the tasks we can help you with:
V-ECU Creation
If the system under test (SUT) is not yet available in the way it is required for SIL, dSPACE supports you in its virtualization with a comprehensive solution portfolio that can be flexibly adapted to your individual situation.
Our solutions cover a wide range of applications, including the generation of V-ECUs for SUTs like these:
- Classic ECUs or functions (AUTOSAR, non-AUTOSAR, various V-ECU levels)
- High-performance computers (HPCs)
- Autonomous driving (AD) functions
V-ECU Integration
As soon as a corresponding V-ECU is available for the SUT, there are different options for integrating it into the SIL simulation.
Depending on the type of V-ECU, you can integrate it, e.g.:
- as an artifact that can be imported directly into VEOS or
- in the form of a co-simulation of several SIL simulation tools.
As a result, you can even integrate SUTs into an overall SIL simulation if they were not originally generated with dSPACE tools or cannot be executed directly on the dSPACE SIL simulation platform VEOS. Of course, you can also reuse existing SUTs and virtualization solutions.
Once the V-ECU is contained in the simulation system, it needs to be connected to the other simulation participants, e.g., a plant model.
Depending on the test requirements, various interfaces are available, including:
- Signal-based communication
- Bus communication
- Various interfaces for high-performance transmission of sensor data
V-ECU Interfacing
Once the V-ECU is integrated, the last step is to access the corresponding SUT in the simulation.
Depending on your requirements, the dSPACE solution offers various options:
- You can access internal variables of the V-ECU via the universal measurement and application protocol XCP or via XIL API.
- For monitoring and controlling bus messages, you can use dSPACE ControlDesk, our experiment and instrumentation software, or a dedicated API.
- Debugging of the V-ECU can be carried out in a standard development environment, e.g., the code editor Microsoft® Visual Studio Code®.
In addition, we offer further options for specific use cases. Please contact us for more information.
Key Benefits of Our Solution for SIL ECU Integration Testing
- Continuous use of artifacts, tools, and tests from SIL to HIL
- Comprehensive solution portfolio for generating and integrating V-ECUs
- Validation of bus traffic, bus timing, and bus planning and testing of error cases, thanks to realistic bus simulation
- High simulation performance
- Easy reproducibility of the tests, even by the developers themselves
- Debugging for simplified troubleshooting
The result: ECU integration tests without real ECU hardware and much earlier in the development process compared to HIL tests.
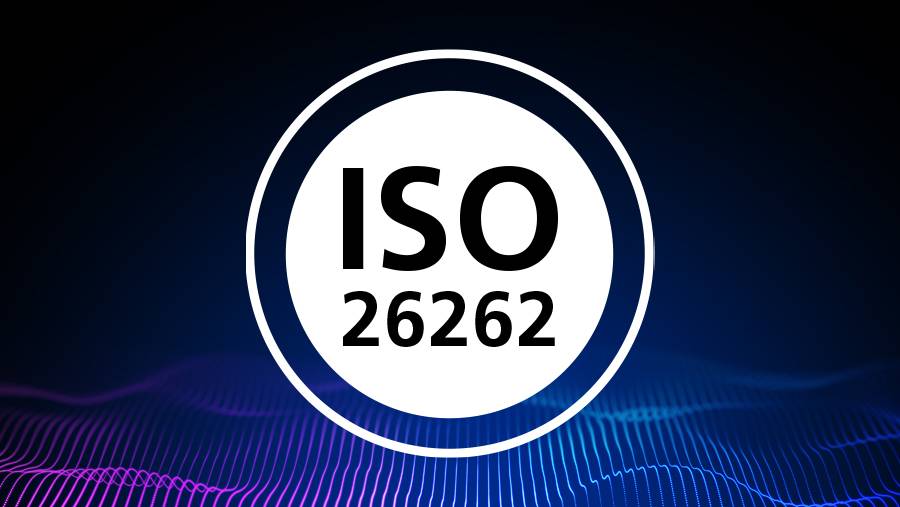
dSPACE VEOS: Certified According to ISO 26262
In the development of safety-critical software, it must be demonstrated and documented that the process and tool chains for development, simulation, and validation deliver trustworthy results. To support our customers with this, VEOS is certified by TÜV SÜD for the testing of safety-relevant systems and for the development of safety-critical functions according to ISO 26262. This allows our customers to exclude VEOS from the qualification of their overall processes according to ISO 26262 and to use it in safety-critical projects without any further effort.